Solutions robotiques pour la logistique des retours
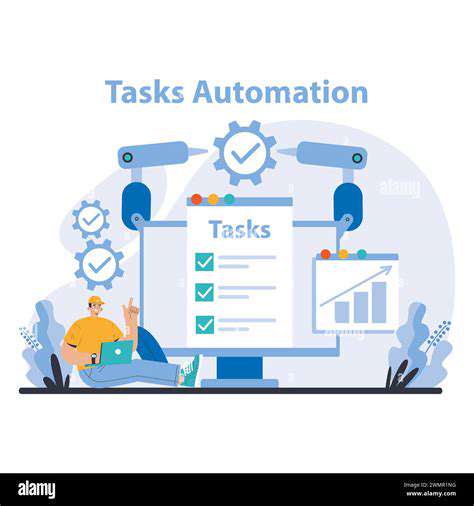
Robotic Process Automation (RPA)
Robotic Process Automation (RPA) is a technology that uses software robots to automate repetitive, rule-based tasks. These software robots, often referred to as bots, can mimic human actions to interact with existing applications. This automation can significantly improve efficiency and reduce errors in various business processes. RPA is particularly well-suited to tasks that follow predefined procedures and involve data entry, manipulation, and communication between different systems.
Implementing RPA can streamline workflows, leading to faster processing times and ultimately, a better return on investment. By automating mundane tasks, RPA frees up human employees to focus on more strategic and value-added activities, which is crucial for business growth and competitiveness.
Improving Accuracy and Consistency
One of the key benefits of robotic automation is the enhanced accuracy and consistency it brings to tasks. Human error is a common factor in many processes, leading to discrepancies and delays. Robotic systems, however, can consistently perform tasks with high precision, eliminating the possibility of human mistakes. By adhering strictly to pre-programmed instructions, robotic automation ensures a high level of reliability and consistency, improving the overall quality of work output.
Automation also reduces the risk of errors associated with manual data entry, calculations, and other repetitive tasks. This results in fewer errors, improved data integrity, and a more trustworthy process.
Increased Productivity and Scalability
Robotic automation significantly increases productivity by handling tasks much faster than human workers. By automating repetitive tasks, robotic systems can operate 24/7, leading to substantial gains in efficiency and output. This increased productivity can be particularly beneficial in high-volume operations, where automation can handle a large workload without any reduction in quality.
Furthermore, robotic automation is highly scalable, making it adaptable to changing business needs. As the volume of work increases, additional robots can be easily deployed to handle the extra workload. This scalability makes robotic automation a valuable asset for businesses experiencing growth or fluctuations in demand.
Cost-Effectiveness and Reduced Operational Costs
Robotic automation can lead to significant cost savings in the long run. By automating tasks, businesses can reduce labor costs associated with human employees performing repetitive work. This reduction in labor costs is a significant factor in the overall cost-effectiveness of robotic automation. Additionally, automation can reduce the need for extra personnel to oversee the tasks, further minimizing operational costs.
The initial investment in robotic automation may seem substantial, but the long-term cost savings and increased efficiency often outweigh the initial outlay. Reduced errors, faster processing times, and optimized workflows contribute to a better return on investment (ROI).
In today's dynamic market, a one-size-fits-all approach often falls short. Businesses and individuals alike are recognizing the value of tailored solutions that address specific needs and objectives. This understanding fuels the demand for customized products and services, moving beyond generic offerings to solutions that are truly optimized for individual circumstances.
Improving Accuracy and Reducing Errors
Optimizing Return Processing with Robotics
Implementing robotic systems for return processing streamlines the entire cycle, from initial customer interaction to final inventory management. Automated sorting and handling of returned goods significantly reduce manual intervention, minimizing human error and ensuring a faster turnaround time. This improved efficiency directly translates to cost savings and enhanced customer satisfaction as returns are processed quickly and accurately.
Robotic arms and conveyor systems can handle a wide variety of packages and product types, regardless of size or weight. This adaptability is crucial in modern logistics, where product variety and return volumes fluctuate. The ability to scale these robotic solutions is essential for companies anticipating growth and an increasing volume of returns.
Automated Sorting and Identification
Robotic systems excel at automating the sorting and identification of returned items. Advanced vision systems enable robots to quickly and accurately read labels, scan barcodes, and recognize product attributes. This automated identification process ensures that returns are routed to the appropriate departments for processing, repair, or restocking, eliminating the need for manual inspection and reducing the risk of misrouting.
By employing sophisticated algorithms and image recognition technology, robots can differentiate between various types of returns, such as damaged, defective, or simply unwanted items. This categorization is vital for efficient inventory management and enables companies to make data-driven decisions regarding product quality and customer preferences.
Enhanced Inventory Management
Robotics play a crucial role in improving inventory management during the return process. Automated systems can track returned items throughout the entire lifecycle, from receiving to processing to storage. This real-time tracking provides visibility into inventory levels and allows for proactive adjustments to meet fluctuating demand and optimize warehouse space.
Integration with warehouse management systems (WMS) allows for seamless data exchange. This data exchange enhances the accuracy of inventory records and enables informed decision-making regarding restocking, reorder points, and overall inventory optimization strategies.
Minimizing Human Error in Handling Returns
Manual handling of returns is prone to errors, including mislabeling, damage during transport, and incorrect data entry. Robotic automation significantly minimizes these errors by removing the human element from many aspects of the return process. This reduction in human error leads to greater accuracy and consistency in processing returns.
Robots operate without fatigue or bias, ensuring that every return is handled with the same degree of care and attention. This consistency is critical for maintaining high-quality standards and building customer trust.
Improved Return Processing Speed and Efficiency
Robotic solutions significantly accelerate the return processing cycle, leading to faster turnaround times for customers. Automation streamlines the entire process, from receiving returned items to final disposition. This speed translates into improved customer satisfaction and reduced operational costs.
The streamlined workflow enables businesses to handle a higher volume of returns efficiently, ensuring that the return process does not become a bottleneck in the overall supply chain. This increased efficiency is critical for companies that rely on quick return processing to maintain a competitive edge.
Reducing Costs Associated with Manual Processing
Investing in robotic solutions for returns logistics offers substantial cost savings in the long run. The automation of tasks previously performed manually reduces labor costs, minimizes the risk of errors, and optimizes warehouse space. This leads to significant savings in operational expenses.
Furthermore, reduced errors and faster processing times result in lower customer service costs. By streamlining the return process, businesses can focus their resources on other core activities and maximize profits. These cost-saving benefits are critical for companies looking to optimize their return logistics operations.
Ensuring Data Accuracy and Tracking
Robotic systems provide a robust framework for data accuracy and tracking throughout the return process. Automated data capture and integration with existing systems ensure that all information related to returns is accurate and readily accessible. This data-driven approach allows businesses to analyze return trends, identify patterns, and make informed decisions to improve future product design and customer service strategies.
The ability to track and trace returns provides valuable insights into the efficiency of the entire process. This insight allows for targeted improvements in various stages of the return cycle, from initial customer interactions to final inventory management. This data-driven approach ultimately leads to a more streamlined and customer-centric return process.
- Comment intégrer les meubles en bois dans le design de votre maison de manière transparente
- Meilleures astuces pour organiser votre maison avec des unités de rangement en bois
- Comment trouver des meubles en bois abordables sans compromettre la qualité ?
- Pourquoi les meubles en bois faits main sont meilleurs que les pièces de production de masse
- Comment choisir des meubles en bois qui complètent l'architecture de votre maison
- Comment entretenir les meubles de jardin en bois par mauvais temps
- Comment choisir des meubles en bois adaptés à votre style de vie
- Comment styliser votre salle à manger avec des meubles en bois
- Comment utiliser le mobilier en bois pour rendre votre maison plus accueillante
- Génération de langage naturel pour les étiquettes et les manifestes d'expédition automatisés
- Jumeau numérique pour l'analyse de fabrication prédictive
- Jumeau numérique pour la gestion de flotte en temps réel