Informations basées sur les données pour une planification de production optimisée
The Importance of Data-Driven Decision Making in Manufacturing
Data Collection and Analysis in Manufacturing
Effective data-driven decision-making in manufacturing hinges on robust data collection and analysis processes. This involves implementing systems that capture relevant data throughout the entire production cycle, from raw material procurement to finished goods delivery. This data encompasses various metrics, including machine performance, production output, quality control results, and even employee efficiency. Sophisticated data analysis tools are then required to process this information, identifying trends, patterns, and anomalies that might otherwise go unnoticed. By meticulously collecting and meticulously analyzing this data, manufacturers can gain valuable insights into their operations, optimizing processes, and ultimately boosting productivity and profitability.
Data collection methods should be standardized and consistent to ensure accuracy and reliability. This includes using automated sensors and monitoring systems to collect real-time data, integrating disparate systems to create a unified data view, and establishing clear protocols for data entry and validation. The resulting data should be stored securely and accessible to authorized personnel. Robust data analysis techniques, such as statistical modeling, machine learning algorithms, and predictive analytics, can be employed to uncover hidden relationships and forecast future trends. This allows manufacturers to anticipate potential problems and proactively implement solutions, leading to more efficient and sustainable operations.
Improving Efficiency and Reducing Costs through Data Insights
Data-driven insights in manufacturing enable significant improvements in efficiency and reduction of costs. By identifying bottlenecks and inefficiencies in production processes, manufacturers can optimize workflows, streamline operations, and eliminate unnecessary steps. This can lead to reduced production time, lower material waste, and improved resource allocation. For instance, analyzing machine downtime data can reveal patterns and causes, allowing for preventative maintenance strategies to be implemented, reducing unscheduled downtime and maximizing equipment uptime. The improved efficiency directly translates into reduced production costs and increased profitability.
Furthermore, data insights can help manufacturers understand customer preferences and demands more accurately. By analyzing sales data, feedback from customer surveys, and market trends, companies can tailor their production to meet specific customer requirements, reducing inventory holding costs and optimizing product offerings. This leads to a more responsive and adaptable manufacturing process, enabling companies to capitalize on market opportunities and maintain a competitive edge.
Finally, data-driven decision-making can lead to a more predictive and proactive approach to quality control. By identifying patterns in quality control data, manufacturers can predict potential defects and implement preventative measures. This proactive approach to quality control reduces the occurrence of defective products, minimizes costly rework or scrap, and enhances the overall quality of the final product. These improvements directly contribute to increased customer satisfaction and brand loyalty.
Analyzing Production Data for Predictive Insights
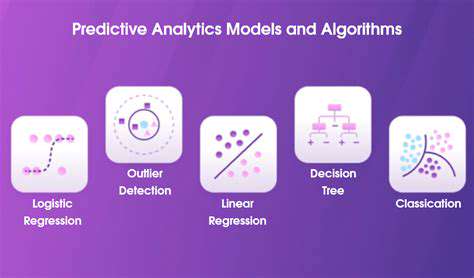
Understanding Production Metrics
Production data analysis is crucial for identifying trends, bottlenecks, and areas for improvement in manufacturing processes. A deep dive into key metrics like output volume, defect rates, cycle time, and equipment downtime provides valuable insights into operational efficiency. Understanding these metrics allows for proactive adjustments and strategies that can significantly impact overall productivity and profitability.
By meticulously tracking and analyzing these metrics, businesses can pinpoint areas where processes are lagging or inefficient. This data-driven approach allows for targeted interventions and optimization strategies. Ultimately, a comprehensive understanding of production metrics is vital for achieving sustainable growth and competitive advantage in the market.
Identifying Bottlenecks and Inefficiencies
Analyzing production data allows for the identification of bottlenecks and inefficiencies within the production workflow. This critical step involves scrutinizing the flow of materials, labor, and equipment utilization across various stages of production. By pinpointing these constraints, businesses can implement corrective actions to streamline the process and enhance overall efficiency.
Pinpointing the exact locations of these bottlenecks is essential for effective interventions. Once identified, targeted improvements can be implemented to address the root cause of the problem, leading to significant improvements in production output and reduced operational costs. A well-defined strategy for addressing bottlenecks is crucial for sustained success.
Predictive Maintenance Strategies
Analyzing historical data on equipment performance, including maintenance records and downtime events, enables the development of predictive maintenance strategies. This proactive approach aims to anticipate potential equipment failures and schedule maintenance before they occur, minimizing unexpected downtime and maximizing operational uptime.
Predictive maintenance models, based on statistical analysis of historical data, can forecast equipment failures with a high degree of accuracy. This allows for optimized scheduling of maintenance activities, leading to significant cost savings and increased equipment longevity. This proactive approach to maintenance is critical for ensuring consistent production output and minimizing disruptions.
Improving Quality Control Processes
Production data analysis plays a vital role in enhancing quality control processes. By tracking defect rates, identifying patterns in faulty products, and analyzing the root causes of quality issues, businesses can implement targeted solutions to minimize defects and improve overall product quality.
Data analysis allows for a more thorough understanding of the factors contributing to defects, enabling the development of preventive measures. This approach to quality control ultimately leads to improved customer satisfaction and a stronger brand reputation. Implementing corrective measures based on data analysis will significantly enhance the overall quality of the finished product.
Optimizing Resource Allocation
Production data analysis allows businesses to optimize the allocation of resources, including raw materials, labor, and equipment. By identifying areas where resources are being utilized inefficiently or wasted, businesses can reallocate resources to maximize production output and minimize costs. This data-driven approach ensures that resources are used strategically and effectively throughout the production process.
Through insightful analysis of production data, businesses can make informed decisions about resource allocation. This optimized resource management leads to greater efficiency, reduced waste, and ultimately, higher profitability. This approach is crucial to maximizing output and minimizing cost overruns.
Forecasting Production Demands
Analyzing historical production data, coupled with market trends and sales forecasts, allows for accurate forecasting of future production demands. This crucial step in the planning process ensures that the production capacity aligns with anticipated demand, preventing shortages or excess inventory. This proactive approach is essential for maintaining a healthy inventory balance and optimizing production workflows.
Accurate forecasting based on historical data and market analysis allows for better inventory management, minimizing storage costs, and maximizing inventory turnover. This precise prediction of future demand also enables optimized production schedules and reduces the risk of stockouts or overstocking. Ultimately, this enables a more responsive and efficient production process.
Implementing a Data-Driven Culture for Continuous Improvement
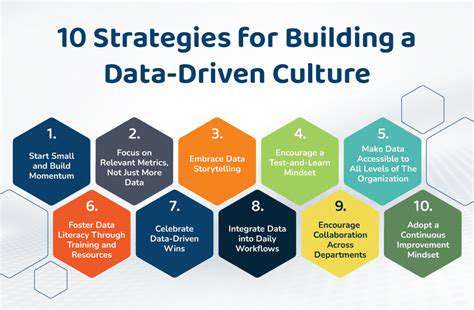
Establishing a Foundation for Data-Driven Decision-Making
A data-driven culture isn't built overnight; it requires a thoughtful and strategic approach that establishes a strong foundation. This involves more than simply collecting data; it necessitates a clear understanding of how that data will be utilized to inform decisions across the organization. Crucially, this means fostering a culture of trust and transparency around data usage, ensuring everyone understands the value and purpose behind data collection and analysis. This includes making sure that data is accessible to those who need it and that the tools and training are available to effectively interpret and utilize the data. Establishing clear data governance policies and procedures is also vital to maintaining data integrity and ensuring compliance.
Understanding the specific needs of different departments and teams is also essential. Each department likely has unique data requirements and ways of working, and these needs must be considered when establishing the data-driven culture. Implementing tailored data solutions that meet these individual needs will empower teams to use data effectively to improve their specific processes and workflows. This tailored approach is more effective than a one-size-fits-all solution, as it directly addresses the specific challenges and opportunities within each department. This personalized approach will foster a sense of ownership and responsibility amongst team members, making them more invested in the success of the data-driven culture.
Cultivating Data Literacy and Analytical Skills
A successful data-driven culture relies heavily on the ability of employees to understand and interpret data. This necessitates a commitment to developing data literacy and analytical skills throughout the organization. This involves providing comprehensive training programs that cover data analysis techniques, data visualization tools, and critical thinking skills related to data interpretation. These programs should be tailored to the specific needs of different roles and responsibilities within the company.
Investing in employee development is critical to long-term success in a data-driven environment. Continuous learning and development are crucial to ensuring that employees can adapt to new technologies and methodologies as they emerge. This includes ongoing training on new data analysis tools and techniques, as well as workshops on data visualization and storytelling. Furthermore, encouraging a culture of experimentation and data-driven problem-solving is key to maximizing the value of data insights.
Encouraging employees to share their data insights and collaborate on data-driven projects will foster a sense of community and shared purpose. This can be achieved through the creation of data-sharing platforms and the organization of regular data-focused workshops and meetings. By actively promoting collaboration and knowledge sharing, the organization can ensure that the value of data insights is maximized throughout the entire enterprise.
- Pourquoi les meubles en bois sont-ils meilleurs pour votre santé et votre bien-être ?
- Comment créer un espace d'inspiration industrielle avec du mobilier en bois
- Les types de bois les plus populaires pour les meubles mid-century modern
- Le guide ultime pour choisir des meubles de jardin en bois
- Les avantages des meubles en bois modulaires pour des espaces de vie flexibles
- Comment associer des meubles en bois à des couleurs et des motifs audacieux ?
- Comment choisir le meilleur bois pour votre design de meubles sur mesure
- Comment combiner des meubles en bois avec une décoration vintage ?
- Meilleurs conseils pour choisir des meubles en bois pour votre bureau à domicile
- Mise en œuvre de la robotique pour les environnements dangereux et les matières dangereuses
- Solutions robotiques pour la logistique des retours
- Le rôle des TI dans la planification et l'exécution stratégiques de la chaîne d'approvisionnement